Carillon Tourbillon Black Obsidian
Discover
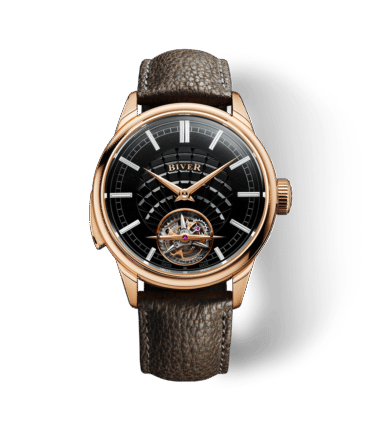
The hands of each Biver watch exemplify our commitment to truly artistic horology, combining an admiration of craft with a deep respect for collectors.
At its most basic level, a watch is a small machine that tells us the time. Whether it is a fine mechanical watch or an inexpensive quartz watch, that essential quality remains the same. But while both accurately count out seconds, minutes, and hours, only one has the ability to make your heart rate quicken and your eyes widen. So what exactly is it that gives a mechanical watch its heart and soul?
We believe this ethereal quality comes from the humanity put into each watch. The hours of hand craftsmanship, the detailed attention to design, and the commitment to doing things “the right way” as its own reward. Each decision, each component is labored over and passes under the eyes of an expert, whose craft and passion are represented in the smallest touches, often unseen and done with an almost spiritual commitment to integrity and a deep respect for the individuals collecting Biver timepieces.
A perfect example of this can be found in the hands that show the hours and minutes in the Carillon Tourbillon. Reading about watches, you will find countless discussions of in-house movements, bracelet construction, and case finishing, but relatively little about the humble hands, despite their importance to any timepiece. “The hands are 80% of what you see when you first look at your watch,” says Jean-Claude Biver. “This is why we spend so much time and energy on them.”
The hands used on the Carillon Tourbillon are much more complex than they first appear. To start, the 18k white gold hands are made of a special alloy called PD210, which contains 21% palladium (significantly more than in standard 18k white gold). This gives them a much brighter, whiter color without the use of any surface treatments or plating. However, it also makes the metal more difficult to work with. The hands must maintain their flat profile, so any bending or deformation during finishing is entirely unacceptable for both mechanical and aesthetic reasons.
And each hand requires multiple finishing steps before it is ready to be mounted in a watch. Each hand has four internal angles, which must be polished by hand, as there is no machine that can mirror-polish an internal angle. That mirror-polish finish extends around the entire beveled edge of each hand and can also be found in the central countersink, while the top surface of each hand is brushed for a more matte look. Even the underside of each hand is either brushed or satin-finished to remove any remaining machining marks and to ensure they don’t cast unwanted reflections on the surface of the watch’s dial.
These special hands symbolize the search for and quest toward perfection.
To achieve this level of finishing on hands made of PD210 was not possible at first. We spent months experimenting with different natural materials for the polishing tools and new ways of working to achieve the desired finishes. It took a lot of trial and error before we landed on the tools and techniques we use today, for both the PD210 and rose gold hands found across the different Carillon Tourbillon variations. When you work with the mind of an artist and refuse to compromise, the results can be quite astounding.
“These special hands symbolize the search for and quest toward perfection,” reflects M. Biver. “This pursuit of perfection means that each day you strive to improve and to get closer to the ultimate goal. At the highest level, it is necessary to move forward not only with the head but also with the heart. You must fall in love both with the process, as well as with the final result.”
This idea of a never ending quest is central to everything we do at Biver. Guided by a mix of engineering and artistry, smarts and sentimentality, we seek to make every watch – and every individual watch component – an expression of this perspective. When you are building watches for eternity, there is no other way.